Aby rozpocząć proces produkcji drewna klejonego, niezbędne jest zgromadzenie odpowiednich materiałów oraz narzędzi. Podstawowym surowcem jest oczywiście drewno, które powinno być starannie wyselekcjonowane pod kątem jakości. Najczęściej używa się gatunków takich jak sosna, świerk czy dąb, które charakteryzują się dobrą wytrzymałością oraz estetyką. Ważne jest, aby drewno było odpowiednio wysuszone, co zapobiega jego deformacji po sklejeniu. Oprócz drewna, kluczowym elementem jest klej, który powinien być dostosowany do rodzaju drewna oraz warunków, w jakich produkt będzie używany. W przypadku drewna klejonego często stosuje się kleje poliuretanowe lub epoksydowe, które zapewniają wysoką odporność na wilgoć i zmiany temperatury. Dodatkowo warto zaopatrzyć się w narzędzia takie jak piła, szlifierka, a także sprzęt do aplikacji kleju. Przydatne będą również zaciski, które pomogą utrzymać elementy w odpowiedniej pozycji podczas schnięcia kleju.
Jakie są etapy produkcji drewna klejonego
Produkcja drewna klejonego składa się z kilku kluczowych etapów, które należy starannie przeprowadzić, aby uzyskać wysokiej jakości produkt. Pierwszym krokiem jest przygotowanie surowca, czyli dokładne wymiarowanie i cięcie desek na odpowiednie długości oraz szerokości. Następnie ważne jest ich wysuszenie do odpowiedniego poziomu wilgotności, co ma istotny wpływ na późniejsze właściwości końcowego produktu. Po przygotowaniu drewna następuje aplikacja kleju na powierzchnie desek, co można zrobić za pomocą pędzla lub specjalnych urządzeń do natrysku. Po nałożeniu kleju deski należy ściśle połączyć i umieścić w zaciskach, aby zapewnić równomierne rozłożenie siły nacisku oraz uniknąć powstawania szczelin. Czas schnięcia zależy od rodzaju użytego kleju oraz warunków otoczenia i może wynosić od kilku godzin do kilku dni. Po zakończeniu procesu schnięcia deski można przeszlifować i dociąć do ostatecznych wymiarów, a także poddać je dalszej obróbce, takiej jak lakierowanie czy malowanie.
Jakie są zalety stosowania drewna klejonego w budownictwie
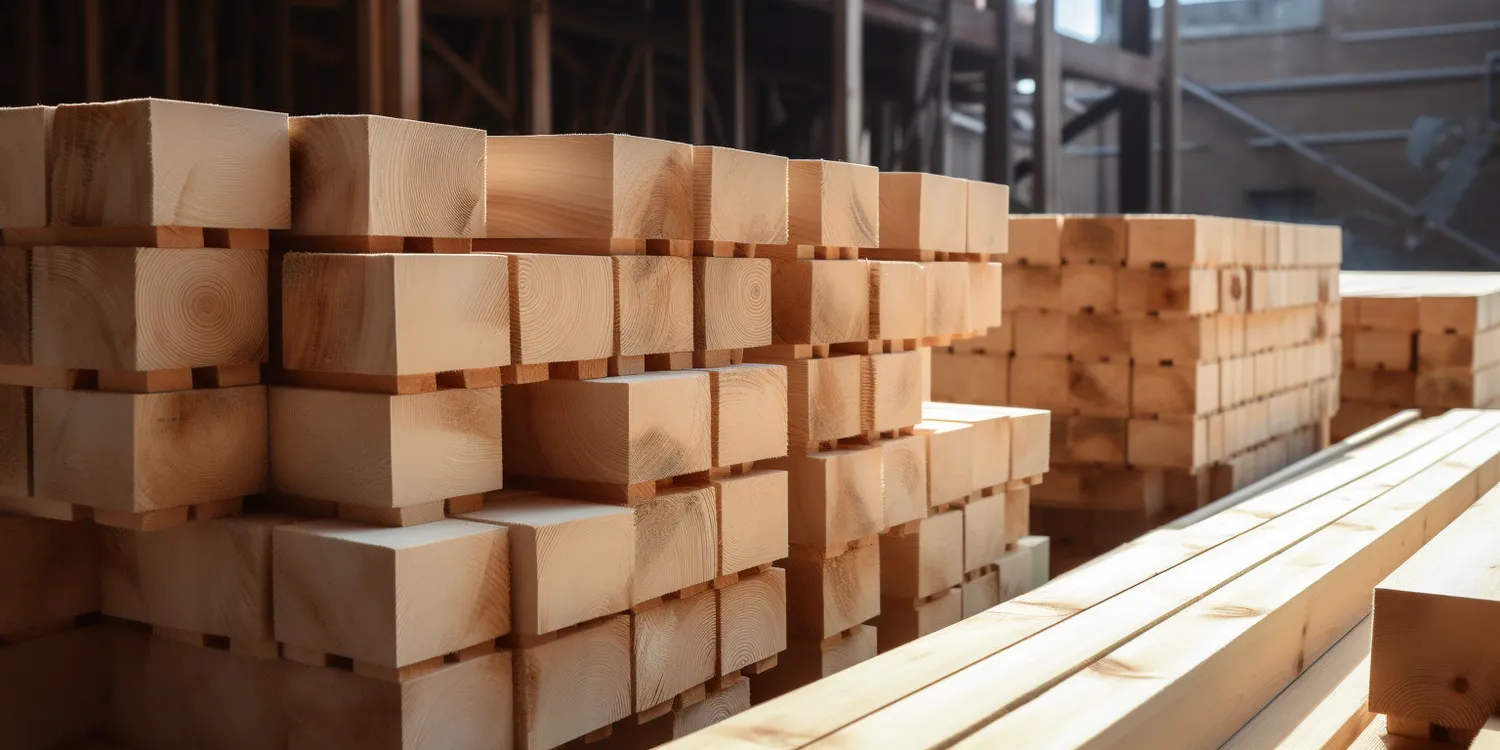
Drewno klejone znajduje coraz szersze zastosowanie w budownictwie ze względu na swoje liczne zalety. Przede wszystkim charakteryzuje się dużą wytrzymałością mechaniczną, co sprawia, że jest idealnym materiałem do konstrukcji nośnych takich jak belki czy słupy. Dzięki procesowi klejenia możliwe jest uzyskanie elementów o znacznych rozmiarach, co pozwala na tworzenie przestronnych konstrukcji bez konieczności stosowania wielu podpór. Kolejną zaletą jest stabilność wymiarowa drewna klejonego – dzięki odpowiedniemu wysuszeniu i sklejeniu elementy te nie ulegają łatwo deformacjom ani pękaniu. Ponadto drewno klejone ma korzystny wpływ na izolację termiczną budynków, co przekłada się na niższe koszty ogrzewania. Warto również zwrócić uwagę na aspekt ekologiczny – drewno jest materiałem odnawialnym i przy odpowiedzialnym zarządzaniu lasami może stanowić zrównoważony wybór dla budownictwa.
Jakie są najczęstsze zastosowania drewna klejonego w praktyce
Drewno klejone znajduje zastosowanie w wielu dziedzinach budownictwa oraz przemysłu meblarskiego ze względu na swoje unikalne właściwości. W architekturze często wykorzystuje się je do budowy dużych obiektów takich jak hale sportowe czy centra wystawowe, gdzie wymagana jest duża przestrzeń bez podpór wewnętrznych. Elementy z drewna klejonego doskonale sprawdzają się również w konstrukcjach dachowych oraz mostach, gdzie ich wytrzymałość i stabilność są kluczowe dla bezpieczeństwa użytkowników. W przemyśle meblarskim drewno klejone wykorzystywane jest do produkcji mebli o nietypowych kształtach oraz dużych gabarytach, ponieważ pozwala na łączenie mniejszych kawałków drewna w większe formy bez ryzyka pękania czy deformacji. Dodatkowo coraz częściej spotyka się drewniane elementy dekoracyjne wykonane z drewna klejonego, takie jak balustrady czy schody, które łączą estetykę z funkcjonalnością.
Jakie są różnice między drewnem klejonym a tradycyjnym drewnem
Wybór między drewnem klejonym a tradycyjnym drewnem ma istotne znaczenie dla wielu projektów budowlanych oraz meblarskich. Drewno tradycyjne, pozyskiwane w postaci pełnych desek, charakteryzuje się naturalnymi właściwościami, ale jest bardziej podatne na deformacje, pęknięcia oraz zmiany wymiarów w wyniku zmian wilgotności i temperatury. W przeciwieństwie do tego drewno klejone, które powstaje z połączenia kilku warstw drewna za pomocą specjalnych klejów, oferuje większą stabilność wymiarową oraz wytrzymałość. Dzięki temu elementy z drewna klejonego mogą być stosowane w konstrukcjach wymagających dużych obciążeń, co czyni je idealnym wyborem dla architektów i inżynierów. Ponadto drewno klejone pozwala na wykorzystanie mniejszych kawałków drewna, co przyczynia się do efektywniejszego wykorzystania surowca i zmniejszenia odpadów. Warto również zauważyć, że drewno klejone często poddawane jest dodatkowym procesom obróbczych, co zwiększa jego odporność na działanie czynników atmosferycznych oraz szkodników.
Jakie są najczęstsze błędy podczas produkcji drewna klejonego
Produkcja drewna klejonego to proces wymagający precyzji oraz staranności, a wiele błędów może prowadzić do obniżenia jakości końcowego produktu. Jednym z najczęstszych błędów jest niewłaściwe przygotowanie surowca; drewno powinno być odpowiednio wysuszone i wolne od wad, takich jak sęki czy pęknięcia. Niewłaściwe cięcie desek może prowadzić do nieprawidłowego dopasowania elementów, co z kolei wpływa na ich wytrzymałość. Kolejnym istotnym aspektem jest aplikacja kleju – zbyt mała ilość lub nierównomierne rozłożenie kleju mogą skutkować słabym połączeniem desek. Ważne jest także przestrzeganie czasu schnięcia; zbyt szybkie usunięcie zacisków przed całkowitym utwardzeniem kleju może prowadzić do deformacji elementów. Dodatkowo nieodpowiednie warunki otoczenia, takie jak zbyt wysoka wilgotność czy niska temperatura, mogą negatywnie wpłynąć na proces klejenia. Dlatego kluczowe jest monitorowanie wszystkich etapów produkcji oraz przestrzeganie zaleceń producenta dotyczących używanych materiałów i narzędzi.
Jakie są koszty produkcji drewna klejonego
Koszty produkcji drewna klejonego mogą się znacznie różnić w zależności od wielu czynników, takich jak rodzaj użytego surowca, zastosowane technologie oraz skala produkcji. Na początku warto uwzględnić koszty zakupu drewna; ceny mogą się różnić w zależności od gatunku oraz lokalizacji dostawców. Następnie należy doliczyć wydatki związane z zakupem odpowiednich materiałów do klejenia oraz narzędzi potrzebnych do obróbki drewna. Koszty te mogą być znaczne, zwłaszcza jeśli planujemy inwestycję w nowoczesny sprzęt do produkcji drewna klejonego. Dodatkowo warto uwzględnić koszty pracy – zatrudnienie wykwalifikowanych pracowników oraz szkolenie ich w zakresie technologii produkcji również generuje wydatki. Warto jednak zauważyć, że chociaż początkowe koszty mogą być wyższe niż w przypadku tradycyjnego drewna, to długoterminowe korzyści związane z wytrzymałością i stabilnością drewna klejonego mogą przynieść oszczędności w przyszłości.
Jakie są najważniejsze normy dotyczące drewna klejonego
Drewno klejone musi spełniać szereg norm i standardów jakościowych, które zapewniają jego bezpieczeństwo oraz trwałość w zastosowaniach budowlanych i meblarskich. W Europie najważniejszym dokumentem regulującym kwestie związane z drewnem klejonym jest norma EN 14080, która określa wymagania dotyczące materiałów kompozytowych wykonanych z drewna. Norma ta obejmuje zarówno aspekty techniczne związane z produkcją i testowaniem elementów drewnianych, jak i wymagania dotyczące ich oznakowania oraz dokumentacji. Warto również zwrócić uwagę na normy dotyczące używanych materiałów klejących; muszą one spełniać określone standardy dotyczące odporności na działanie wilgoci oraz substancji chemicznych. Dodatkowo producenci powinni przestrzegać zasad dotyczących ochrony środowiska oraz zrównoważonego zarządzania zasobami leśnymi. Certyfikaty takie jak FSC (Forest Stewardship Council) czy PEFC (Programme for the Endorsement of Forest Certification) potwierdzają odpowiedzialne pozyskiwanie surowców oraz ich zgodność z normami ekologicznymi.
Jakie są przyszłe trendy w produkcji drewna klejonego
Przemysł drzewny i produkcja drewna klejonego przechodzą dynamiczne zmiany związane z nowymi technologiami oraz rosnącą świadomością ekologiczną społeczeństwa. Jednym z głównych trendów jest rozwój technologii cyfrowych, które umożliwiają automatyzację procesów produkcyjnych oraz precyzyjne monitorowanie jakości surowców i gotowych produktów. Dzięki zastosowaniu sztucznej inteligencji możliwe staje się optymalizowanie procesu produkcji pod kątem wydajności oraz minimalizacji odpadów. Kolejnym istotnym trendem jest wzrost zainteresowania materiałami ekologicznymi; coraz więcej producentów stawia na wykorzystanie surowców pochodzących z certyfikowanych lasów oraz ekologicznych metod produkcji. Również innowacyjne technologie obróbcze pozwalają na tworzenie nowych rodzajów drewna klejonego o unikalnych właściwościach mechanicznych i estetycznych. W miarę rosnącej popularności budownictwa pasywnego i energooszczędnego, drewno klejone staje się coraz bardziej pożądanym materiałem ze względu na swoje doskonałe właściwości izolacyjne oraz estetykę naturalnego surowca.
Jakie są metody testowania jakości drewna klejonego
Testowanie jakości drewna klejonego jest kluczowym etapem zapewniającym bezpieczeństwo i trwałość produktów końcowych. Istnieje wiele metod oceny jakości tego materiału, które obejmują zarówno badania laboratoryjne, jak i testy praktyczne przeprowadzane na gotowych elementach konstrukcyjnych. Jedną z podstawowych metod jest badanie wytrzymałościowe polegające na poddaniu próbek różnych obciążeń w celu określenia ich nośności oraz odporności na deformacje. Testy te mogą obejmować zarówno statyczne obciążenia punktowe, jak i dynamiczne cykle obciążeń symulujące warunki eksploatacyjne. Inną ważną metodą jest ocena jakości połączeń klejowych; badania te mają na celu sprawdzenie siły adhezji między warstwami drewna a zastosowanym klejem. Dodatkowo przeprowadza się analizy wizualne mające na celu wykrycie ewentualnych wad surowca takich jak sęki czy pęknięcia, które mogą wpłynąć na jakość końcowego produktu. Wiele laboratoriów korzysta także z nowoczesnych technologii obrazowania takich jak tomografia komputerowa czy ultradźwięki do dokładnej analizy struktury wewnętrznej próbki drewna.